When the designed gear transmission works under unstable load or the two-phase meshing gears are all hard tooth surfaces (HB>350), in order to make the failure not concentrated on certain gear teeth and scrapped in advance, one of the gears should be used. Any tooth of a gear has an equal chance of meshing with any tooth of another gear that meshes. In this case, the selection principle of the gear ratio is: the number of teeth of the two gears is relatively prime. Generally, the common divisor of adjacent gear teeth is required to be as small as possible, so that the deformation on one tooth can be evenly ground to as many teeth as possible.
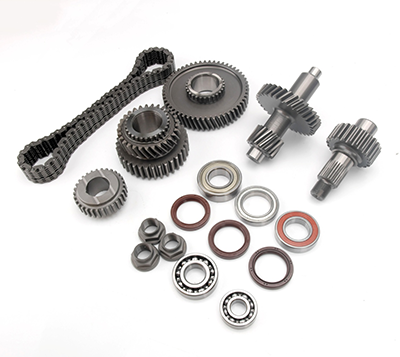
When the designed gear transmission works under unstable load or the two-phase meshing gears are all hard tooth surfaces (HB>350), in order to make the failure not concentrated on certain gear teeth and scrapped in advance, one of the gears should be used. Any tooth of a gear has an equal chance of meshing with any tooth of another gear that meshes. In this case, the selection principle of the gear ratio is: the number of teeth of the two gears is relatively prime. Generally, the common divisor of adjacent gear teeth is required to be as small as possible, so that the deformation on one tooth can be evenly ground to as many teeth as possible.